|
 |
P
& G Game |
 |
-
Policy |
|
[The following solution was derived
from the original Harvard Business Review Case Studies. There
are other possible solutions, but the following one yields
stable long run minimum costs. See
also one of these alternate solutions just developed, at
the end of this one.]
The
solution to the P&G soap packaging line simulation is
based on answers to the following four questions:
- At what
level should the original production level be set?
- When should
a change in production level be made?
- How much
should the change be?
- How do
we plan for the plant shutdown for vacation?
We will start with the third
question. Since the cost of changing production is relatively
high, we will make the largest possible change possible,
+/- 10 units, so as to spread this cost over as many units
as possible and cut down on the number of changes.
We will now consider the second
question – when to change the level of production.
The key variable is the ENDING INVENTORY. We are dealing
with three types of variables – controllable (PRODUCTION
LEVEL), uncontrollable (DEMAND) and the dependent variable
(ENDING INVENTORY). The following relationship shows the
connection.
Beginning Inventory + Production – Demand
= Ending Inventory.
The Ending Inventory of one
period is the Beginning Inventory of the next period.
Since the average weekly demand
is 100, we would like the Ending Inventory to be around 100.
This would be viable if the demand was steady. However, the
standard deviation of demand is 30 units. This means the
demand from week to week could vary between 70 and 130 about
2/3rds of the time, between 40 and 160, 95% of the time and
between 10 and 190, 99.8 % of the time. Such variation
is difficult to handle. A measure of variation used is the ‘Coefficient
of Variation’ – defined as the ratio of the standard
deviation to the mean.
COV = STD DEV /
MEAN
If this measure is less than
5%, then the variation is can be considered ‘noise.
If it the between 5 and 15 %, this is considered somewhat
variable. About 15%, the variation is considered WILD. Our
value is 30%! So we have a problem. This coupled with the
two week delay in changes going into effect can cause severe
problems, mainly large shortages. Therefore, we need to establish ‘control
limits’ in the value of Ending Inventory. These limits
are similar to those used in Quality Assurance Control Charts.
If
the Ending Inventory is around 100, we will want our production
to be 100. As Ending Inventory exceeds 100, we will want
to have less production so as to ‘boil off’ the
excess inventory and get back to 100 and reduce our inventory
holding cost.
If
the Ending Inventory is less than 100, we will want to increase
production to avoid stock-outs and the high penalty costs.
Below is a possible set of limits
based on the original P&G case study. The numbers on
the left describe the ending inventory and the numbers in
the middle give the desired production level for ranges of
the ending inventory. |
 |
|
This
chart also answers the first question. Since the initial
inventory available is 270 units, this is way above the upper
most limit and we set the initial production level at 70
units.
As
the demand for each week is known, we can determine the ending
inventory. (Actually, the simulation does it for you.) When
the ending inventory falls below 190, the table indicates
that we need to increase production – by 10 units.
To
illustrate the use of this chart, we have summarized the
first dozen weeks of an actual simulation below
|

|
|
Since
the beginning inventory is 270, we set the initial production
level at 70. At the end of the first week with a demand of
130, the ending inventory is still above 190 so we make no
change. In week 2 the demand is 142 and the ending inventory
is reduced to 132. By the chart we want the production level
to be 90, so we increase production by 10. Note, this will
raise it only to 80 so we may have to raise it again in the
next week. (To keep track of where we are, we can simply
Put a token on the chart at production level 80.) (A coin
will do – a penny or dime for current production.)
The
next week demand is low – only 62 and the ending inventory
is still in the 130-160 range for a production level of 90.
But we are still at 80, so we raise it again. In the next
four weeks, the demand is relatively high and the ending
inventory falls to a low of 47. So each week we raise it
by 10 until we are at the 130 level. This ‘catch-up’ takes
effect and ending inventory starts to rise and as it does
and enters a new range, we start to lower production with
-10 changes. We would continue using this strategy throughout
the simulation.
At
this point, it appears that we have made an excessive number
of production changes. The alternative is to make fewer changes
and the result could be disastrous. With the two week delay
in implementing the production level change and with the
greatly varying demand, the ending inventory could sink to
extremely low levels and recovery could take weeks. It is
better to exercise more precise control.
The
other tendency is to relax when changes are made. For example,
if the ending inventory were to barely move into a new range,
say from 155 to 162, the urge may be to delay making a change.
Again this could be bad. The idea is to make these changes
almost automatic, i.e. program a computer to do them.
The
final question is, ‘How to prepare for the plant shutdown
in weeks 26 and 27 when no production is possible. We know
that during this two week period, the average total demand
should be 200. While it is possible that we could have two
weeks of extremely high or extremely low demand, this is
not likely. (The standard deviation for this two period of
demand is 42.42. So 2/3rds of the time the two demand would
range from 158 to 242 and 95% of the time from 115 to 285.)
What
we need to do is build up a ‘buffer’ inventory
of 200 units to cover this period. The way we do this is
to ‘set aside’ 10 units a week for 20 weeks.
We do this by ‘subtracting’ this increasing buffer
from the actual inventory to arrive at an ‘effective’ inventory
and base our decision of production change on this amount.
We start this in week 6 and continue to week 25.
|
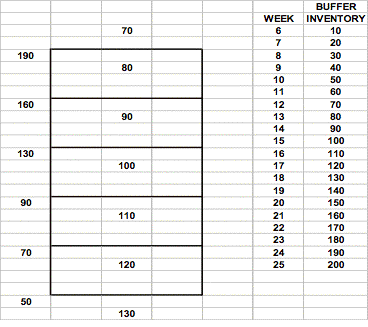
|
|
To illustrate the use of this
table, we again show a portion extracted from the simulation,
below. |

|
|
In
this simulation, we have generated the same random sequence
for demand as before, so that we can compare with our previous
analysis. The production changes are the same thru weeks
1
– 5.
In
week 6, we begin to use the ‘Effective Inventory.’ However
this does not result in any different from before. It is
in the 8th week that a difference occurs. The
effect of the buffer inventory is to show the effective inventory
still at a low level. Therefore, we delay the change to decrease
production. A comparison of the two is shown below.
The
overall impact of using this strategy, is to keep product
levels high to build up the buffer inventory to prepare for
the plant shutdown. This has two effects. First inventory
costs will be slightly higher. Second, the probability of
a stock-out will be lower especially as we get closer to
the plant shut-down when the buffer becomes large. So the
possible stock-out cost is reduced.
Employing
this solution method does not guarantee a shortage will not
occur. The total cost will vary from simulation run to run.
With this method, the average total inventory cost is around
$135,000. The lowest seen is $65,000 and values near $250,000
are not unusual. Without using a good strategy, some users
have had costs approaching one million.
This
is not the only effective strategy. We have seen one about
as good, but it has been lost for decades. Perhaps you will
rediscover it or one even better.
William
G. Lesso
October
20, 2006
|
The
following solution was developed by
Mr. Hiroki Abe
Offshore
Iwaki Petroleum Co
Ltd.
|
|
During
a recent workshop (Dec, 2006), Mr. Abe was asked to play
the PNG games several times. After the first play, he was
asked to develop a strategy, write it down and play the game
again using his strategy. This strategy, given below, is
quite simple and gave consistently good results. You might
want to try it.
- Set
initial production at 100.
- All
production changes are to be only +/- 5.
- Let
Ending Inventory build up to the300-350 range by increasing
production.
- Keep
it in this range by +/- production changes until after
the plant shutdown.
- After
the plant shutdown, keep Ending Inventory in the 100-159
range until
the end of the game.
I do not recall if Mr. Abe specified
and upper or lower limits to production levels but I believe
the changes in production should keep overall production
between 70 and 130 or perhaps between 50 and 150 if one is
adventurous
|
|
|
|